AHMED Tawfik
United Kingdom – 44-7909455120 (land line)
AHMED Tawfik khamis al-naimi kha.alnaimi@yahoo.com
salsam350@hotmail.com
Engineering
Topic: Collage 5 Essays
Details:
college foundation program
1-005 Electrical and Electronic Principles Assign 3.
2-006 HS assignment brief for overseas 2012.
3-007 Business Management Techniques Assign 3.
4-065 Utilisation of Electrical Energy Assign 3.
5-001 Analytical Methods Assign 3.
——————————————
Unit 7: Business Management Techniques for Engineers
Assignment 3 –Planning and Control
Student Name: __________________________
Unit Tutor Assessor Signature Date Assessed
R Hyde
Grading Criteria
Pass Achieved Merit Achieved Distinction Achieved
3.1 M1 N/A D1 N/A
3.2 M2 N/A D2 N/A
3.3 M3a N/A D3
4.1 M3b N/A
4.2 M3c
4.3
Assignment Author IV signature
(brief) IV signature
(assessment)
R Hyde Dr Muhammed Al-Asadi
ASSESSMENT FEEDBACK
Note: the Notional Score is for formative feedback purposes only. 5 is allocated as sufficient for meeting the criteria, less than 5 is an indication of extra work required, more than 5 is an indication extra work included.
PASS grade must be achieved:
Outcomes Learner has demonstrated the ability to: Source of evidence Tutors comments Notional Score (10)
Outcome 3
Understand the key functions of financial planning and control
LO3.1:Explain the financial planning process in an engineering business
Task 1
LO3.2:Examine the factors influencing the decision-making process during financial planning
Task 2
LO3.3:Analyse standard costing techniques
Task 3
Outcome 4
Be able to apply project planning and scheduling methods to an engineering project
LO4.1:Establish the project resources and requirements
Task 4
LO4.2:Produce a plan with appropriate time-scales for completing the project
Task 5
LO4.3:Plan the human resource requirement and costs associated with each stage of the project
Task 6
MERIT grade descriptors that may be achieved for this assignment:
Merit Grade Descriptors Indicative Characteristics Source of evidence Tutors comments Notional Score (10)
M1
Identify and apply strategies to find appropriate solutions
n/a
M2
Select/design and apply appropriate methods/techniques
n/a
M3c
Present and communicate appropriate findings
Throughout the report, the solutions are coherently presented using technical language appropriately and in a professional manner
All Tasks
Distinction grade descriptors that may be achieved for this assignment:
Merit Grade Descriptors Indicative Characteristics Source of evidence Tutors comments Notional Score (10)
D1
Use critical reflection to evaluate own work and justify valid conclusions
n/a
D2
Take responsibility for managing and organising activities
n/a
D3
Demonstrate convergent/ lateral/ creative thinking
Careful consideration of a greater number of factors affecting financial planning.
Task 2
General Information
All submissions to be electronic in MS Word format with a minimum of 20 typed words. All answers must be clearly identified as to which task and question they refer to. All work must be submitted through Learnzone.
Task 1 – Learning Outcome 3.1
Explain the financial planning process in an engineering business
Q1: In order to achieve its objectives and profit targets, an engineering business must have in place an adequate financial plan. Explain the main steps in forming a financial plan for a typical engineering company.
(350 words)
Task 2 – Learning Outcome 3.2
Examine the factors influencing the decision-making process during financial planning
Q2: Several factors will influence the directors of an engineering company in formulating the financial plan. List and examine three of these factors and discuss what effect they might have on the decision making process during the financial planning.
(300 words)
Task 3 – Learning Outcome 3.3
Analyse standard costing techniques
Q3: Mega Widgets Ltd have designed a new Super Widget which may revolutionise inter-stellar sandwich making.
Production costs:
Variable, material, labour etc: £10 per item
Fixed, machinery, tolling heating etc £20,000 per year
Administration + selling overheads:
Fixed: £35,000
The company have to decide whether to make the widgets and sell them. Calculate the selling price based on absorption and marginal costing techniques. The company wish to make a 40% profit on each unit.
Analyse the most appropriate costing method if production is at a rate of 100 widgets per hour and sales are predicted to be 20,000 per year.
(300 words + calculations)
For the following three tasks, use the following information:
You have been passed some notes from an initial project planning meeting after a design breakthrough. You have been tasked with preparing the feasibility study.
Super Widget Manufacturing Project
To manufacture the new super widget requires 3 manufacturing processes and a packing process. Quotations for the machinery have been obtained.
1. Squidging machine, £10k, 2 operators, 50 units per hour, maintenance 6 month intervals @ 4hours, running cost £25/ hour
2. Banging machine, £20k, 1 operator, 100 units per hour, maintenance yearly @ 8hours, running cost £30/ hour
3. Thumping machine, £5k, automated, 200 per hour, maintenance monthly @ 1hour, running cost £10/ hour
4. Packing process, current equipment can be used, 1 operator, 20 units per hour, maintenance by operators daily @ 30 minutes.
Installing the machines takes 1 half day each and requires 1 electrical and 1 mechanical fitter.
Training takes 1 hour per operator and requires the machine being available.
Commissioning each machine takes 2 days, requires both fitters and 1 operator.
Production is to be spread evenly across the year, with batches produced in a single run, once per week.
Labour costs are £10 per hour per operator, £15 per hour for fitters.
Task 4 – Learning Outcomes 4.1
Establish the project resources and requirements
Q4:List the total resources and associated costs required to complete the whole project for a 2 year production run.
Task 5 – Learning Outcomes 4.2
Produce a plan with appropriate time-scales for completing the project
Q5: Produce a project plan covering installation, commissioning, training and operating production for the two years.
Task 6 – Learning Outcomes 4.3
Plan the human resource requirement and costs associated with each stage of the project
Q6:Plan the human resources required listing the requirements on a weekly basis and costs on a monthly basis.
End of assessment brief
——————————
Loughborough college
Unit 6: Health & Safety and Risk Assessment
Assignment – international students only
Student Name: __________________________
Unit Tutor Assessor Signature Date Assessed
J A D Melville J A D Melville
Grading Criteria
Pass Achieved Merit Achieved Distinction Achieved
1.1 M1 D1
1.2 M2 D2
1.3 M3 D3
2.1
2.2
2.3
3.1
3.2
3.3
3.4
4.1
4.2
4.3
4.4
4.5
Assignment Author IV signature
(brief) IV signature
(assessment)
J A D Melville
ASSESSMENT FEEDBACK
Note: the Notional Score is for formative feedback purposes only. 5 is allocated as sufficient for meeting the criteria, less than 5 is an indication of extra work required, more than 5 is an indication extra work included.
PASS grade must be achieved:
Outcomes Learner has demonstrated the ability to: Source of evidence Tutors comments Notional Score (10)
Outcome 1
Be able to select and apply safe working procedures to engineering operations.
LO1.1:Select and justify choice of protective clothing and equipment to ensure personal protection in a given environment.
Task 1
LO1.2:Evaluate a range of permit-to-work systems and identify isolation requirements for given applications.
Task 1, 2
LO1.3:Use monitoring equipment to ensure the promotion of a safe working environment.
Task 1
Outcome 2
Understand the nature and use of current health and safety legislation.
LO2.1:(a) Identify industrial work areas where current regulations would apply and (b) describe the role of the HSE inspectorate.
Task 2
LO2.2:Implement a schedule for the setting up of a safety audit system.
Task 2
LO2.3:Select the relevant codes of practice to enhance safety.
Task 2
Outcome 3
Be able to analyse engineering activities for the assessment of risk
LO3.1:Identify a hazard and produce a risk rating.
Task 3
LO3.2:Evaluate frequency and severity of an identified hazard.
Task 3
LO3.3:Produce a hazard proforma for a given application.
Task 3
LO3.4:Analyse a recording system that tracks and highlights potential hazards.
Task 4
Outcome 4
Be able to manage and minimise risk to life, property and engineering activities within an industrial environment.
LO4.1:Evaluate evidence that would specify the existence of a risk or risks.
Task 4
LO4.2:Analyse the implications of the risk and the effect on life, property and activities.
Task 4
LO4.3:Obtain and use accurate information on the risk for protection of others.
Task 4
LO4.4:Produce a report on how best to minimise the risk to people, property and activities and recommend effective methods of implementation and control.
Task 4
LO4.5:Identify routes and methods of implementation within a company to ensure that compliance with codes of practice and regulations pertaining to the risk are fully understood.
Task 4
MERIT grade descriptors that may be achieved for this assignment:
Merit Grade Descriptors Indicative Characteristics Source of evidence Tutors comments Notional Score (10)
M1
Identify and apply strategies to find appropriate solutions
Use of appropriate sources to identify appropriate legislation, regulations and codes of practice
M2
Select/design and apply appropriate methods/techniques
Appropriate recommendations for action made
M3
Present and communicate appropriate findings
The report is coherently presented using technical language appropriately and in a professional manner
Distinction grade descriptors that may be achieved for this assignment:
Merit Grade Descriptors Indicative Characteristics Source of evidence Tutors comments Notional Score (10)
D1
Use critical reflection to evaluate own work and justify valid conclusions
Justification of recommendations
D2
Take responsibility for managing and organising activities
All elements appropriate to the intended audience, linked to legislation where required, achieved independently of undue support.
D3
Demonstrate convergent/ lateral/ creative thinking
Critical understanding of the implications of H&S on business and vice versa
General Information
All submissions to be electronic in MS Word format with a minimum of 20 typed words. All answers must be clearly identified as to which task and question they refer to. All work must be submitted through Learnzone.
Case Study 1
An oil storage tank is located below ground level. Access is by one hatch in the top. The tank has been drained and has been out of use for some time. An inspection is to be carried out on the condition of the tank base and it has already been identified that welding will be necessary at one location.
Task 1, Learning Outcomes 1.1, 1.2, 1.3
Be able to select and apply safe working procedures to engineering operations.
Describe in detail a procedure where the tank can be inspected and welded safely. Consider what aspects of the environment require monitoring and how that will be achieved. Identify any personal protective equipment required and any procedures to be followed to ensure the safety of any operative(s) during the inspection and welding operation.
Deliverables: This can be bullet points or a report, with justification of any recommendations for equipment or procedures. Maximum 600 words.
Case Study 2
An engineering workshop contains five pillar drills, six milling machines and six lathes, all powered by 3-phase 415V. Up to twelve people may be undertaking manufacturing operations in there in a normal working day.
Task 2, Learning Outcomes 2.1, 2.2, 2.3
Understand the nature and use of current health and safety legislation.
(a) Identify all the UK legislation, regulations and relevant codes of practice which must be complied with to ensure the safety of personnel in the workshop.
(b) Describe the role of the Health and Safety Inspectorate in respect of day-to-day management of Health and Safety and in the event of an accident.
(c) Create a bullet-point list of all the aspects of the workshop which should be considered in a Safety Audit, and suggest how often each aspect should be audited.
Deliverables: A report for the first part, which must clearly state which documents you consider relevant. Maximum 600 words. The second part should be a list of aspects to be inspected, with a suggested frequency for each.
Case Study 3
A cement plant has multiple operations, each of which is controlled by PLCs which are controlled from a central control room in a different building. One of the PLCs for the stone-crushing operation has malfunctioned; it is located inside a cabinet on the wall in the crusher house. It requires replacement.
Task 3, Learning Outcomes 3.1, 3.2, 3.3
Be able to analyse engineering activities for the assessment of risk.
Using the template in the Appendix at the end of this document, start a Risk Assessment for the operation of replacing the PLC. Consider three of the main hazards and complete the template for those only.
Deliverables:Completed Risk Assessment.
Case Study 4
A distribution warehouse for a manufacturing company has vehicles both delivering and collecting from one end and movement of both fork-lift vehicles and people in the main warehouse area. Routes for the road vehicles, lifts and pedestrians are segregated. The company are proposing to undertake a study into the warehouse to make the operation safer, after one worker sustained a minor injury in a collision with a fork-lift truck.
Task 4, Learning Outcomes 3.4, 4.1, 4.2, 4.3, 4.4, 4.5
Be able to manage and minimise risk to life, property and engineering activities within an industrial environment.
Write a report for the company management outlining a strategy for the study. Suggest three different sources of safety / accident data to base the study on and explain how the data can be used to identify hazards and analyse the risks. Explain how the risk analysis can be developed into an action plan for the workplace and suggest how this can be implemented, including any staff training which might be required, and how and when the process should be reviewed.
Deliverables: A report on the strategy for risk reduction. Actual data and detailed recommendations are not required. Maximum 400 words.
Useful resources:http://www.hse.gov.uk/
Essentials of Health and Safety at Work (free download from HSE website)
Health and Safety at Work etc. Act 1974
Management of Health and Safety at Work Regulations 1999
Workplace (Health, Safety and Welfare) Regulations 1992
Provision and Use of Work Equipment Regulations 1998
Control of Substances Hazardous to Health Regulations 2002
Noise at Work Regulations 2005
Electricity at Work Regulations 1989
Health and Safety in Engineering Workshops (free download from HSE website)
Five Steps to Risk Assessment (free download from HSE website)
All the free downloads from the HSE website are also located on LearnZone. Provide references for all sources of information.
APPENDIX : RISK ASSESSMENT
Location:
Type of Risk Assessment
Date:
Review Date:
Assessor:
Assessment carried out with assistance from:
Date:
Safety Officer Initial
Risk Rating: Probability x Severity = Risk Level
P= Probability of Accident Occurring
Score Probability Score Severity
1 Very Unlikely 1 Injury Unlikely
2 Unlikely 2 Minor Injury- First aid
3 Possible 3 Injury requiring Hospital Treatment
4 Likely 4 Major Injury
5 Extremely Likely 5 Possible Death or Permanent Disability
S=Severity of likely injuries Scoring and actions:
Overall score Risk rating Action
1-5 Low No immediate action (keep under review)
6-10 Moderate Action to be taken to recify faults
11-15 Medium Action required within 3 months
16-25 High Urgent action required to reduce the risk
Risks with the highest score should be given the highest priority
Additional comments:
Ref No. Task/ Hazard Identified Associated Risks Existing Control Measures Persons
at Risk P S Risk Rating Comments
Remedial Action Required (include any other types of RA required)
Ref.
No. Recommendations Agreed Actions / reasonably practicable Person/s responsible Agreed
timescale Final risk rating Completed and verified: To be completed by Safety Officer
———————————
Unit 65: Utilisation of Electrical Energy
Assignment 3 –Circuit Protection and Polyphase Motors
Student Name: __________________________
Unit Tutor Assessor Signature Date Assessed
Grading Criteria
Pass Achieved Merit Achieved Distinction Achieved
2.1 M1 N/A D1 N/A
2.2 M2 D2 N/A
2.3 M3a N/A D3
5.1 M3b N/A
5.2 M3c
5.3
Assignment Author IV signature
(brief) IV signature
(assessment)
S Johnston Muhammed Al-Asadi
ASSESSMENT FEEDBACK
Note: the Notional Score is for formative feedback purposes only. 5 is allocated as sufficient for meeting the criteria, less than 5 is an indication of extra work required, more than 5 is an indication extra work included.
PASS grade must be achieved:
Outcomes Learner has demonstrated the ability to: Source of evidence Tutors comments Notional Score (10)
Outcome 2:
Understand the applications of circuit protection for distribution and installation systems
LO2.1: Explain the construction of over-current protection devices
Task 1, parts i, ii, iii
LO2.2:Explain the operating principles of circuit over-current protection devices
Task 1, parts i, ii, iii
LO2.3:Explain the operating principles of earth fault protection devices
Task 1, parts iv, v
Outcomes Learner has demonstrated the ability to: Source of evidence Tutors comments Notional Score (10)
Outcome 5:
Understand the operation of a polyphase induction motor
LO5.1: Describe the types and explain the construction of induction motors
Task 2
LO5.2:Explain the operating principles and methods of starting induction motors
Task 3
LO5.3:Analyse the methods of speed control of induction motors
Task 4
MERIT grade descriptors that may be achieved for this assignment:
Merit Grade Descriptors Indicative Characteristics Source of evidence Tutors comments Notional Score (10)
M2
Select/design and apply appropriate methods/techniques
The explanation for the operating principles has been extended to include a slip-torque curve
Task 3, question 3
M3c
Present and communicate appropriate findings
Throughout the report, the solutions are coherently presented using technical language appropriately and in a professional manner
All Tasks
DISTINCTION grade descriptors that may be achieved for this assignment:
Distinction Grade Descriptors Indicative Characteristics Source of evidence Tutors comments Notional Score (10)
D3
Demonstrate convergent/lateral/creative thinking
Significant detail on the operation of Inverters has been included and consideration of the benefits and dis-advantages has been fully explored
Task 3 question 4 and Task 5
General Information
All submissions to be electronic in MS Word format with a minimum of 20 typed words. All answers must be clearly identified as to which task and question they refer to. All work must be submitted through Learnzone.
Task 1 – Learning Outcomes 2.1, 2.2 and 2.3
Explain the construction of over-current protection devices
Explain the operating principles of circuit over-current protection devices
Explain the operating principles of earth fault protection devices
1. Explain, with the aid of diagrams, the construction and operating principles of the following types of protection devices:
a. Airblast circuit breaker
b. Oil-filled circuit breaker
c. High rupture capacity fuse
d. Residual current device
e. Earth fault relay
Task 2 – Learning Outcome 5.1
Describe the types and explain the construction of induction motors
2. Describe the construction of the following types of three-phase induction motors; you may use diagrams to aid your description.
a. Single cage
b. Double cage
c. Wound rotor
Task 3 – Learning Outcome 5.2
Explain the operating principles and methods of starting induction motors
3. Explain the operating principles of a three-phase cage rotor induction motor. Your explanation must include the terms:
a. Rotating magnetic field
b. Mutual inductance
c. Slip
d. Synchronous speed
e. Torque
4. The following are all methods of starting a three-phase induction motor. In each case, explain how the starting method works, state the type of motor the starter is used on, and a typical power range for that motor.
a. Direct-on-line
b. Star-Delta
c. Inverter / soft start
Task 4 – Learning Outcomes 5.3
Analyse the methods of speed control of induction motors
5. Describe and analyse two different methods of controlling the speed of three-phase induction motors.
End of assessment brief
————————————–
Unit 1: Analytical Methods
Assignment 3 – Modelling Engineering Situations Using Statistics and Probability
Student Name: __________________________
Unit Tutor Assessor Signature Date Assessed
Grading Criteria
Pass Achieved Merit Achieved Distinction Achieved
4.1 M1 N/A D1
4.2 M2 N/A D2
4.3 M3a N/A D3
4.4 M3b N/A
M3c
Assignment Author IV signature
(brief) IV signature
(assessment)
S Johnston Thanuja Goonetilleke
ASSESSMENT FEEDBACK
Note: the Notional Score is for formative feedback purposes only. 5 is allocated as sufficient for meeting the criteria, less than 5 is an indication of extra work required, more than 5 is an indication extra work included.
PASS grade must be achieved:
Outcomes Learner has demonstrated the ability to: Source of evidence Tutors comments Notional Score (10)
Outcome 4
Be able to analyse and model engineering situations and solve problems using statistics and probability
LO4.1:represent engineering data in tabular and graphical form
Task 1, parts a, b, c, and d
LO4.2:determine measures of central tendency and dispersion
Task 1, parts e, f
LO4.3:apply linear regression and product moment correlation to a variety of engineering situations
Task 2
LO4.4:use the normal distribution and confidence intervals for estimating reliability and quality of engineering components and systems
Task 3
MERIT grade descriptors that may be achieved for this assignment:
Merit Grade Descriptors Indicative Characteristics Source of evidence Tutors comments Notional Score (10)
M3c
Present and communicate appropriate findings
Throughout the report, the solutions are coherently presented using technical language appropriately and in a professional manner
All Tasks
DISTINCTION grade descriptors that may be achieved for this assignment:
Distinction Grade Descriptors Indicative Characteristics Source of evidence Tutors comments Notional Score (10)
D1
Use critical reflection to evaluate own work and justify valid conclusions
A discussion on how this information would be used in a manufacturing context is fully justified.
Task 1 and/or Task 3
D2
Take responsibility for managing and organising activities
An alternative regression method has been used to estimate the hardness and conclusions have been drawn as to the accuracy of both methods.
Task2
D3
Demonstrate convergent/ lateral/ creative thinking
A discussion has been included to consider the usefulness of the different techniques used to gather information in the assignment.
All Tasks
General Information
All submissions to be electronic in MS Word format with a minimum of 20 typed words. All answers must be clearly identified as to which task and question they refer to. All work must be submitted through Learnzone.
Task 1 – Learning Outcomes 4.1 and 4.2
Represent engineering data in tabular and graphical form
Determine measures of central tendency and dispersion
1. The masses of 50 castings were measured. The results in kilograms were as follows
4.6 4.7 4.5 4.6 4.7 4.4 4.8 4.3 4.2 4.8
4.7 4.5 4.7 4.4 4.5 4.5 4.6 4.4 4.6 4.6
4.8 4.3 4.8 4.5 4.5 4.6 4.6 4.7 4.6 4.7
4.4 4.6 4.5 4.4 4.3 4.7 4.7 4.6 4.6 4.8
4.9 4.4 4.5 4.7 4.4 4.5 4.9 4.7 4.5 4.6
a. Arrange the data in 8 equal classes between 4.2 and 4.9kilograms.
b. Determine the frequency distribution.
c. Draw the frequency histogram and frequency polygon.
d. Calculate the mean, median and interquartile range.
e. Calculate the standard deviation for the data. You may wish to use a coded method.
f. Calculate the limits within which you would expect (i) 95% and (ii) 99% of components to fall.
Task 2 – Learning Outcomes 4.3
Apply linear regression and product moment correlation to a variety of engineering situations
2. Following the machining process the components are to be hardened and then tempered. As part of the design process a sample of eight components was tempered at different temperatures with the following results:
Temperature °C Hardness Vpn
240 550
275 532
300 525
335 514
360 474
395 470
420 458
455 446
a. Draw a scatter diagram of this data and calculate the correlation coefficient. Comment on the nature of the relationship between temperature and hardness.
b. Use least-squares linear regression analysis to establish an equation with which hardness can be predicted from temperature for this particular steel.
c. Use the equation found above to estimate the hardness values for temperatures of 260°C and 370°C.
d. Comment on the accuracy and reliability of estimates that may be obtained using the preceding analysis.
Task 3 – Learning Outcome 4.4
Use the normal distribution and confidence intervals for estimating reliability and quality of engineering components and systems
3. A machine produces components whose diameters should be distributed Normally with mean 0.15 cm and Standard Deviation 0.01 cm. It is suspected that the mean may have changed over a long period of use.
To test for this possibility, a sample of 150 components is drawn and the mean is computed at 0.147. Using the assumption that μ is true, determine whether there is any evidence at the 5% level that the mean of the components has changed.
4. The blanks are to be machined to the component profile. The machining equipment can only accept blanks which are no more than 120mm wide and 500mm long.
The probability of the length being greater than 500mm is 2.5% (0.025) and the probability of the width being greater than 120mm is 3% (0.03).
a. Calculate the probability of a blank being oversize in both dimensions.
b. Show that the probability that a blank is unacceptable (i.e. is oversize in either dimension) is 0.05425.
c. Use the binomial distribution to find the probability that two blanks selected at random from a sample of six will be oversize, if the probability of a blank being oversize in either dimension is 0.05425.
d. Use the Poisson distribution to find the probability that two blanks selected at random from a box of 20 will be oversize, using p = 0.05425 as above.
End of assessment brief
————————————–
Unit 7: Business Management Techniques for Engineers
Assignment 3 –Planning and Control
Task 1 – Learning Outcomes 3.1: Explain the Financial Planning Process in an Engineering Business
These are the steps for a typical financial plan for an engineering company business;
1) Gathering of Information
This is a very important part of the process as it gives the business owner about the prevailing market conditions for the products or services to be offered. This is also the point at which the owner establishes the goals for the engineering company. Some legal and financial documents are also involved in this stage and they include budgets, financial statements, attorney documents, tax returns and so on.
2) Information Analysis And Plan Development
This is where the collected information and goals are brought together into a concrete plan. In developing the action steps for the engineering firm, you look into insurance for machines and equipment, review liabilities and assets, look at the income for the firm and investments as well.
3) Presenting The Plan
In this step, the various stakeholders of the engineering firm are given the plan for discussions and recommendations. This is the goals and expectations of the firm are reviewed, and additional questions are raised. Whoever is drafting the finance plan must ensure that those running the firm understand fully about every bit of the plan, otherwise it might be too difficult to implement it.
4) Plan Implementation
This is where the engineering firm starts acquiring all the investments that will enable it carry out the mandate. If there is need to sell some of the investments, this is also done at this step. Habits in terms of saving and spending are also changed. The core aim of this step is to ensure that the objectives of the engineering firm are met.
5) Performance Monitoring
With the full understanding that a financial plan for an engineering firm might not be perfect, the quality of the services or products offered must be reviewed. This advices the management of the firm whether there might be need for any corrective action.
6) Review and Revise The Plan To Attain Goals
The financial planning process ought be reviewed and reviewed constantly with the full understanding that engineering market circumstances are bound to change. This plan will be reviewed until the financial goals laid are achieved.
Task 2- Learning Outcome 3.2: Examine the Factors Influencing the Decision-Making Process during Financial Planning
In looking at factors that will influence decision making process during financial planning for an engineering company, a number of guidelines for this process come into focus. Firstly, each financial planning exercise is unique for each engineering firm. This means that there is no way a plan from another company can suit a seemingly similar one. Another thing that the directors will look into is how simple the financial plan is. In this planning, simplicity is the key. Simplicity in this case refers to the financial products the directors intend to use to meet their goals. Another winning strategy the directors of the firm need to consider is being realistic in their plan. In an engineering firm, directors are most likely dealing with a long term goal. In such a scenario, the directors should employ diversification of financial products.
Having considered the factors unique to the firm, it becomes imperative to analyse the external factors that could affect the financial planning decisions. The political stability or instability is a major factor which the directors may not have control over. Taking the main issues at play here as growth of the economic and social issues, the government of the day will determine how financial products perform. The economic performance of the country will also affect financial planning. Only after analysing the economic cycle will the directors make sound financial plans for the engineering company. Talking of the economic cycle, interest rates are a crucial consideration for any business. The prevailing interest rates will determine the growth rate of a business. In this line, the directors will seek to know the inflation rate.
These days, whenever directors sit to discuss financial plans they will in most cases look into the bigger picture, which is the global issues. For example in an engineering firm, the unstable oil prices are a big problem. This is a global issue but its effects trickle down to most parts of the world.
Task 3-Learning Outcome 3.3: Analyse Standard Costing Techniques
Marginal costing and absorption costing are the two techniques used to calculate cost. Although the two methods are used for costing, they have some fundamental differences that might be useful for this case. So let us look into the basics of the two methods.
Marginal costing is applicable for costing where variables are considered. The absorption costing method is a bit different because it covers both variables and fixed costs. What are variable costs? Variable costs for Mega Widgets Limited are not constant and they include material, labour etc. On the other hand, fixed costs are fixed costs don’t usually change and may be used for financial projections of the firm.
Marginal costing method is easier than absorption costing. However, this makes the approach less accurate as it looks at only one aspect.
Fixed costs:
Fixed, machinery, tolling £20,000 per year
Administration + selling overheads: £35,000 per year
Total fixed cost £55,000
Variable cost per unit £10
Budgeted sales units 20,000
Marginal costing
Total contribution required=total fixed costs+ required profit
The selling price per unit is £14(40% profit on variable cost per unit)
Contribution per unit is 14-10 which is £4
Total fixed costs=£55,000
For breakeven the firm must sell 13,750 units (£55,000/£4)
From this method, the breakeven units are less than the budgeted sales units.
Absorption costing
Variable materials and labour= £10 per item per unit
Fixed selling +administration overhead=£35,000=£1.75
Fixed machinery, tolling, heating etc=£20,000=£1
Unit product cost=£10+£1.75+£1=£12.75
Adding 40% profit gives £17.85
Therefore, target selling price per unit is £17.85.
Task 4-Learning Outcomes 4.1: Establish the Project Resources and Requirements
Resources and Requirements for the Project
Machine Resource Requirement in terms of cost/amount
Squidging machine Cost £10,000
Operators 2
Production 50 units per hour
Running £25 per hour
Maintenance 16 hours
Banging machine Cost £20k
Operator 1
Production 100 units per hour
Maintenance 16 hours
Running £30 per hour
Thumping machine Cost £5k
No operator(automated)
Production 200 units per hour
Maintenance 24 hours
Running cost £10
Packing Use current equipment
Operator 1
Production 20 units per hour
Maintenance 30 minutes daily
Task 5-Learning Outcomes 4.2: Produce a Plan with Appropriate Time-Scales for Completing the Project
Project Plan
Activity Start Finish
Machine installation, training, and commissioning of machines January 1st 2013 January 15th 2013
Maintenance of squidging machine June 15th 2013 June 15th 2013
Maintenance of banging machine January 15th 2014 January 16th 2014
Maintenance of squidging machine January 15th 2014 January 15th 2014
Maintenance of squidging machine June 15th 2014 June 15th 2014
Task 6-Learning Outcomes 4.3: Plan the Human Resources Requirement and Costs Associated With Each Stage of the Project
Human Resource Plan
Assuming machine runs (1 day) 24 hours in a week
Machine Weekly Requirement(s) Monthly Running Cost
Squidging machine 2 operators £2400+£480=£2880
Banging machine 1 operator £2880+£240=£3120
Thumping machine Automated £960
Packing machine 1 operator £240
Place an order today and get 13% Discount (Code GAC13)
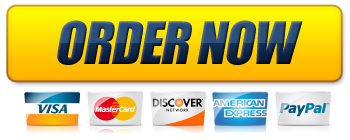