Scope of Project
You must develop a manufacturing plan to machine the part to the final dimensions. The company is a small company of about 30 workers currently.
Product Design
You will design 1 tensile test bar using the following diagram
Develop a part print WITH tolerancing for this part
Material Cost
The raw material will be steel 1045 that I specify. It will come as 1 diameter bar stock at a length you specify ( the dimensions you can find it on the picture that I uploaded with the order)
Labor Cost
The labor cost for your plant is $15 per hour for all employees, except maintenance personnel, which cost $22 per hour.( it may more than one worker or it may a team of workers)
Volume
Your manufacturing facility must provide 200,000 of the tensile test specimens
The equipment will be a stand alone cell or line. No other parts will flow though this area at this time.
Operational Plan
The facility is scheduled to operate 250 days per year and run two 8 ½ hour shifts per day. The workers must be given 30 minutes for lunch and two 15-minute breaks. The product life cycle is expected to be 5 years or more.
Reports
Reports must be written using a word processor and spreadsheet when appropriate. All drawings must be completed using CAD.
1) Title Page (minimum one page)
2) Table of Contents ( minimum three pages)
3) Executive Summary (1-2 pages)
4) A written report detailing the manufacturing plan. The individual manufacturing deliverables must support all information presented in the manufacturing plan summary.
i) Part prints (components plus assembly)
ii) Initial investment required and projected cost per part
iii) Conclusions, Recommendations
5) Manufacturing Plan Deliverables including all supporting data
Manufacturing Plan Deliverables
TAKT Time Calculations – TAKT is a German word for pace. TAKT time is the rate at which your customer requires the product. TAKT time defines the manufacturing line speed and the cycle time for the manufacturing operations. TAKT time is computed as:
Available work time per day / Daily required demand (parts/day)
Design Cycle Time Calculations – Design cycle time is the cycle time at which you design your manufacturing operations after considering contractual breaks, setup time, planned maintenance, estimated downtime, reject rates, etc. All of the items above reduce your actual work time available per day and reduce the required cycle time. Each team must also consider the reject produced by the system and increase the required production to offset the loss. The team must report the manufacturing cells planned operational availability. Operational availability is the Planned operating time /Available work time.
Process Plan Block Diagram – After reviewing the product prints, develop a process plan block diagram that represents the product flow through the various machines and processes. Include equipment, material handling, material flow, quality checks, repair loops, etc..
Equipment Sequence of Operations and Balance Chart – Develop a detailed step-by-step sequence of operations for each process or piece of equipment. Calculate the time required for each cut or step in the process. This document is required to determine if the operation can produce parts at the required rate. Do not forget to include operator load and unload times. When the sequence-of-operation charts are complete, use a graph to compare the cycle time of each process against the design cycle time for the line. The line should be balanced without any process above or well below the design cycle time of the line.
Tooling – A list of all cutting tools with holders must be specified. Also include speeds and feeds. Be specific
Fixture – A fixture concept must be specified. This does not have to be drawn
Machining Equipment Specifications – Select the actual machines required to produce the parts including manufacture and model number. Make sure the machines can meet the required horsepower, federates, and spindle speeds to make the cuts. Investigate the standard work holding device, turret and spindle supplied with the machine and make sure the selected tooling will mate appropriately. Consider the following factors: tool change time, MCU manufacturer, machine work envelope, machine footprint, cost, HP, etc…. Also specify the required chip removal system. Include any sales information you deem helpful on why you made your choice.
Cost Estimate – Develop a detailed cost estimate of the initial investment required to purchase and install the manufacturing cell. Then determine the approximate unit cost of the product based on your manufacturing cell design. Include the following items in your calculations:
a) Direct Material Cost – Include the initial purchase price of each component ($/unit).
b) Direct Labor Cost – Calculate the total labor cost per shift divided by the number of parts produced per shift ($/unit).
c) Burden Rate – The manufacturing facility has a burden rate of 250%. The burden rate includes such items as employee benefits, taxes, insurance, etc… Multiple the direct labor cost per unit (item b) by the burden rate to determine the burden rate cost per piece ($/unit).
d) Depreciation Cost – Use straight-line depreciation to determine the impact of the initial investment. Assume the usable life of the equipment is 5 years with a salvage value of 15% at the end of the life span. Divide the initial cost minus the salvage value by five to determine the depreciation cost per year. Divide the annual depreciation cost by the annual volume to determine the cost per piece ($/unit)
e) Add all of the above items together to determine the estimated unit cost of the product.
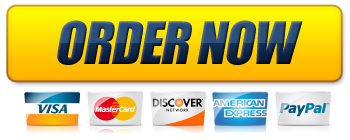