29
Manufacturing strategy of General Dynamics Electric Boat – Seamless Deliverable
Order Instructions:
Master of Business Administration
Module: AUSM27E Manufacturing Strategy
Assignment Title: Individual Coursework
Assignment Weighting : 100%
Description of Assignment
Case study: General Dynamics Electric Boat – Seamless Deliverable
Source: US DoD (2007) Design for Production (2) Seamless Deliverable [online] available from
[24 April 2013]
General Dynamics Electric Boat was founded in 1899, and has established standards of excellence in the design, construction and lifecycle support of submarines for the U.S. Navy. Primary operations are the shipyard in Groton, Connecticut, the automated hull-fabrication and outfitting facility in Quonset Point, Rhode Island, and an engineering building in New London, Connecticut. The current workforce is more than 11,000 employees.
In 2007, Electric Boat conducted an independent study to reduce the ship production cycle time and costs after winning a contract to build the Virginia Class Submarine (VCS) program. Studies have shown ship design processes are not keeping pace with state-of-the-art manufacturing practices. Identified challenges at the shop floor include:
• Poor coordination among work cell operations,
• Lack of timely, accurate and electronic data,
• Outdated design and construction 3D modelling system,
• Delays are pushing costs up beyond the allocated budget,
• Poor work flow and construction sequence resulting in wastages,
• Outdated or wrong drawings for production, and
• Frustration leads to finger pointing among staff and turnover.
The stakeholders are willing to further invest into the infrastructure at the shop floor to integrate work cells seamlessly. Hence, Operation Seamless Deliverable was initiated with the objective to reduce waste and production cycle time.
Brief
The case study is discussed on week 2 during the start of the new trimester. Students are required to work independently to identify areas for improvement, technology to streamline the operation and estimated investment needed to fulfil the objectives set in Operation Seamless Deliverable within a period of 2 years. The exact name of all proposed technology must be named for example, Mentor Graphics SystemVision (Aerospace) instead of 3D CAD/CAM. Details of the identified technology system can be submitted as appendices.
From a helicopter view, students are expected to draw and present a proposal to organise, implement and manage these changes within the given timeline. You are given 6 weeks to prepare and present your proposal for approval by stakeholders (starting week 9).
Resources
Reading materials are given as per the Module Descriptor of this module. Internet resources are given below but not exhaustive.
1. Manufacturing Engineering News: http://www.sme.org/manufacturingengineering/
2. Manufacturing Technology News: http://www.manufacturingnews.com/
3. Manufacturing Journal: http://www.emeraldinsight.com/products/journals/journals.htm?id=jmtm
4. Production Technology: http://businesscasestudies.co.uk/business-theory/operations/production-technology.html#axzz2RLX3hcmx
5. Production Technology for Aquaculture: http://www.aquaculture.co.il/
6. General Dynamics Electric Boat: http://www.gdeb.com/
7. US DoD Manufacturing Technology Program: https://www.dodmantech.com/award/successes/index.asp
Avoid using any of the online sources given below:
www.wikipedia.org, www.netmba.com, www.marketingteacher.com, www.marketingtutor.com, www.mindtools.com, www.quickmba.com, www.ezinearticles.com, www.soopertutorials.com, www.wisegeek.com, www.slideshare.com, www.ehow.com, www.scribd.com, www.howstuffwork.com, www.12manage.com, www.marketance.com, www.helium.com, www.biztech91.com, www.marketing91.com, www.referenceforbusiness.com, www.highn.me, www.ideafinder.com, www.drypen.in, any blogs / blogspot, and any unreliable and/or non-academic sources.
Working Arrangements
• Students are expected to write not more than 3,500 words in this report on an individual basis.
• Should students have any doubts or questions, they may contact or write to their lecturer/tutor for clarification. In the event when the lecturer/tutor is on leave or outstation, student may leave a message to the lecturer/tutor at the Student Services Counter.
• Class Presentation (10 marks) shall be conducted by each student. Marks will be awarded as follows:
o Contents 4
o Showmanship 1
o Clarity and flow of thought 2
o Quality of PPT slides 1
o Keeping Time 1
o Closure 1
Major Deliverables (Individual Assignment)
• Written Report as part of coursework 90%
• Class Presentation as part of coursework 10%
The purpose of the assessment is to evaluate student’s understanding of the course materials and his/her ability to apply the acquired knowledge to the type of problems that may be encountered in the working environment.
Upon the completion of this module, students must achieve the following intended learning outcomes:
1. Appreciate the process of setting corporate / company objectives and of crafting strategy.
2. Understand the basic content of, and recognize and appreciate the significance of, the linkages between marketing, manufacturing and corporate / company strategy.
3. Understand the concepts underpinning the theory of manufacturing strategy and how a manufacturing strategy can contribute to business performance and competitive advantage.
4. Evaluate individual elements of a manufacturing strategy and with this knowledge / capability, be able to apply a conceptual framework or methodology for its development / refinement.
5. Demonstrate capability to potentially improve a company’s business performance. This capability will be evident through the successful application to the assignment case study of theory, knowledge and appropriate analytical and deductive skills developed during the module. The outcome will be justified improvements to the strategies of the case manufacturing company.
Submission instructions
• Check your name and Student ID are clearly written. Auston is not responsible for any assignment submitted without clearly written name or Student ID. Such unknown assignment will not be marked or graded.
• Your assignment should be typewritten in either Arial or Times New Roman font, size 11 and 1½ line spacing.
• Adopt Harvard Referencing Style throughout your report. (see Coventry University guidelines at url – http://www.coventry.ac.uk/study-at-coventry/student-support/academic-support/centre-for-academic-writing2/support-for-students/academic-writing-resources/cu-harvard-reference-style-guide/?theme=main)
• You are to indicate on your Preface page, which business template or format you have chosen for your report.
• Include Table of Contents and insert page number at every page.
• Finished report must be submitted together with the Mark sheet clearly filled in, the turnitin similarity report and the Auston Acknowledgement Form available from the counter staff.
• Drop your finished report in the drop-box located at the Auston foyer. A penalty of 5% of the total mark will be deducted for each day late after the submission date (refer to your Student Handbook). This applies for a maximum of three (3) days (including Saturday and Sunday), after which the assignment will not be accepted.
• CD containing the assignment softcopy in Microsoft Word 2010 is to be attached
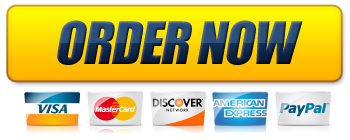